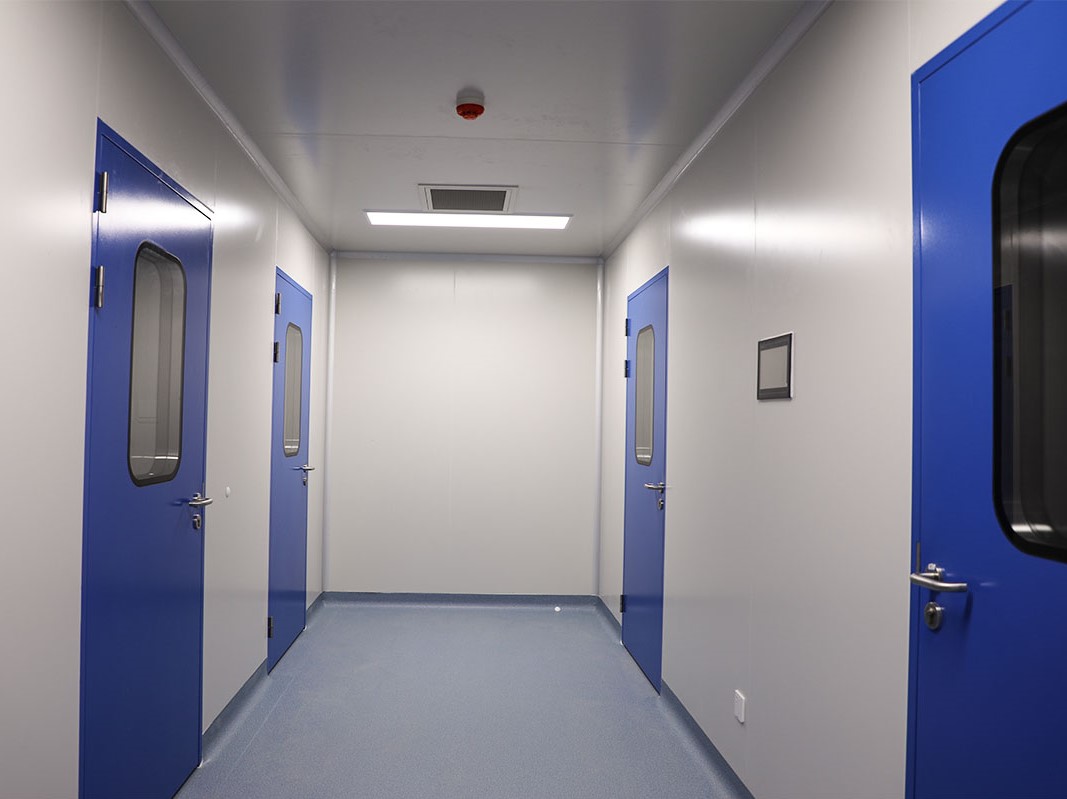
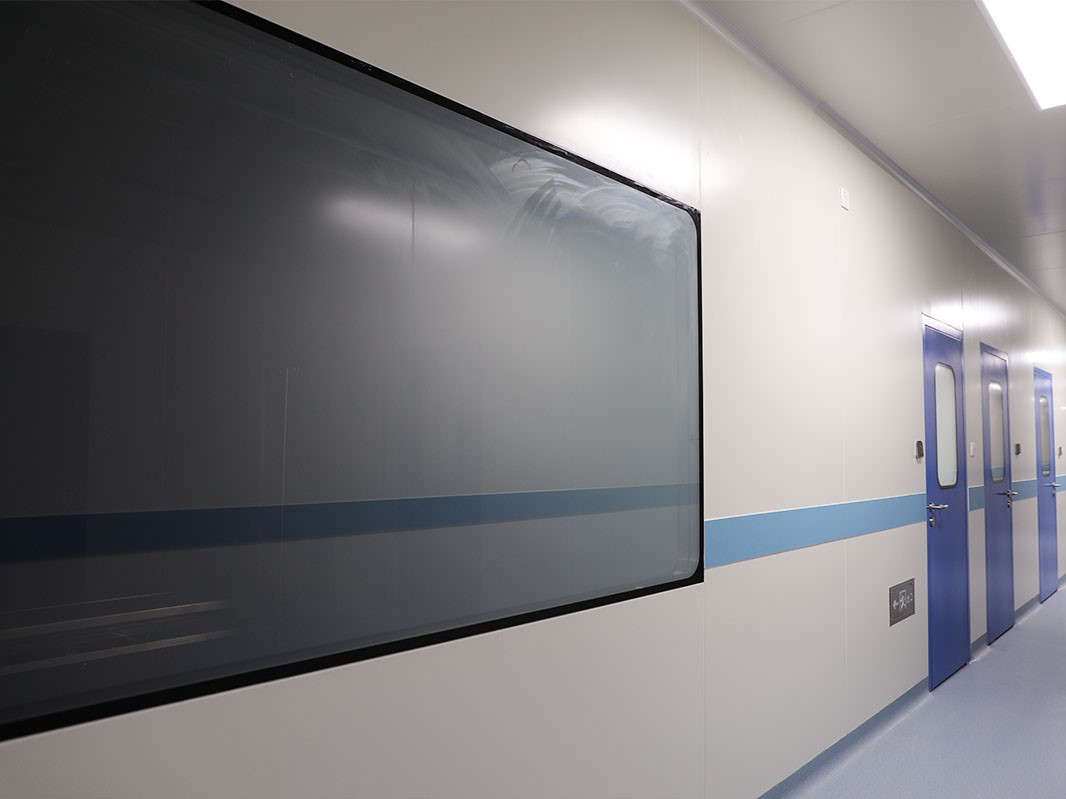
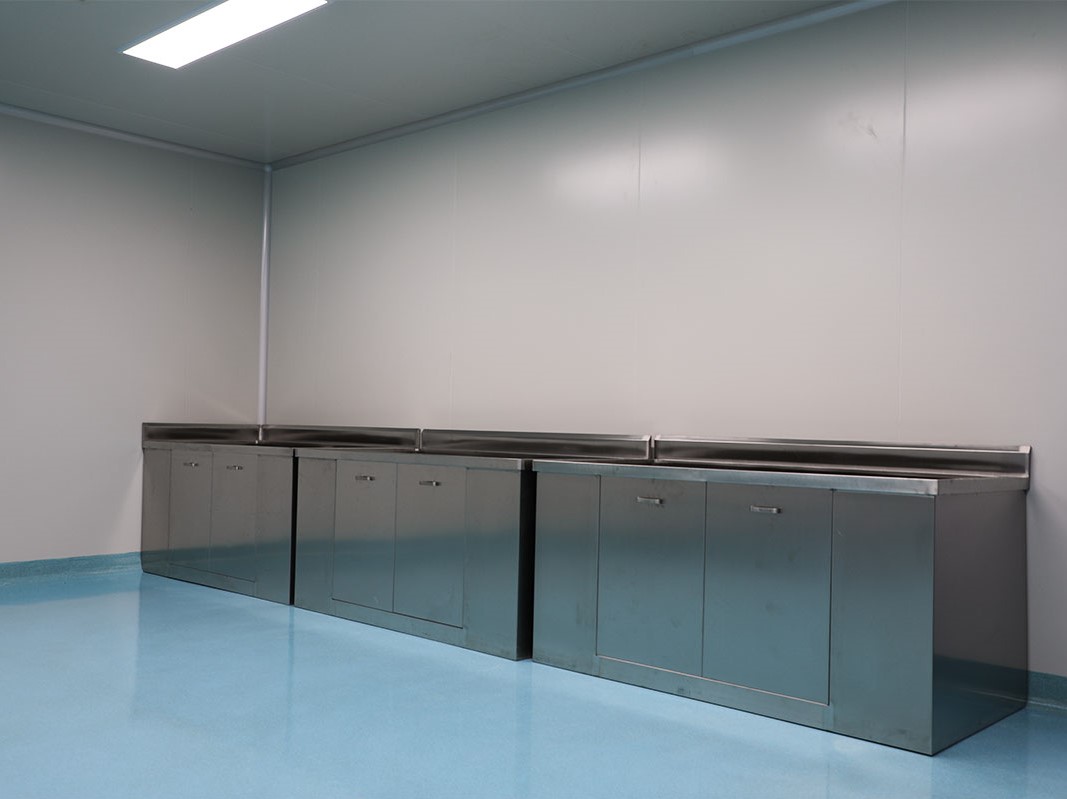
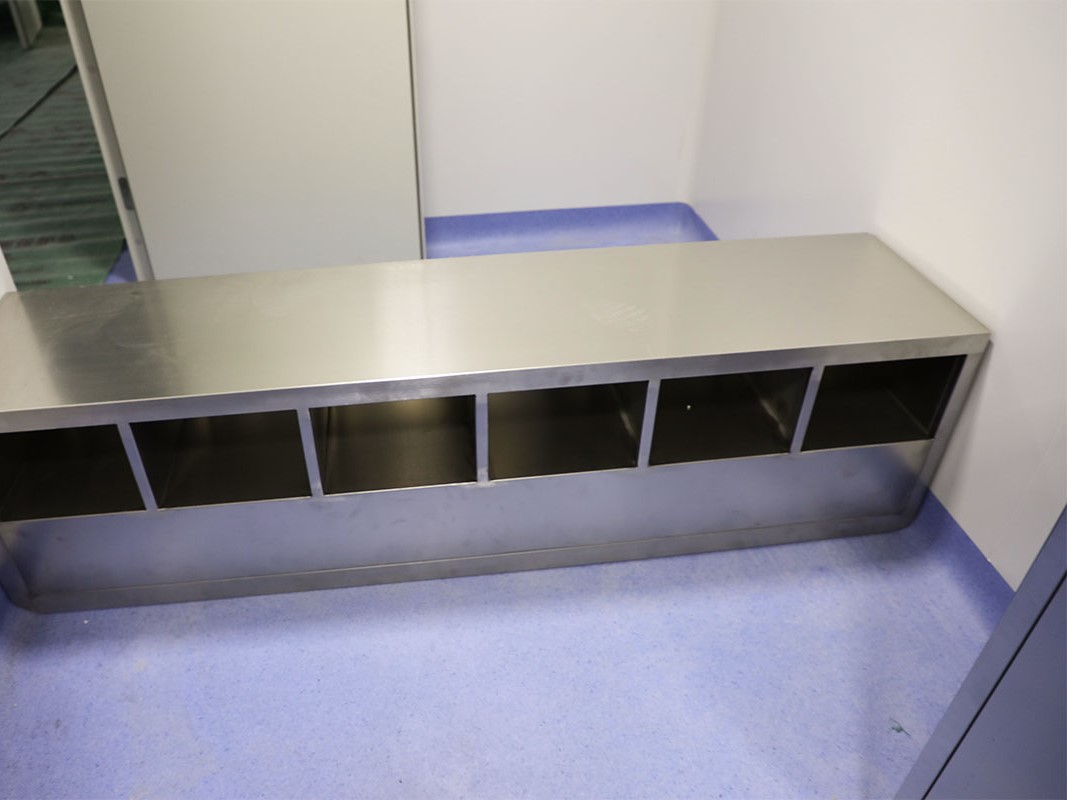
1992 में इसके प्रचार के बाद से, चीन के फार्मास्युटिकल उद्योग में "गुड मैन्युफैक्चरिंग प्रैक्टिस फॉर ड्रग्स" (जीएमपी) को धीरे -धीरे फार्मास्युटिकल प्रोडक्शन एंटरप्राइजेज द्वारा मान्यता प्राप्त, स्वीकार और कार्यान्वित किया गया है। जीएमपी उद्यमों के लिए एक राष्ट्रीय अनिवार्य नीति है, और उद्यम जो निर्दिष्ट समय सीमा के भीतर आवश्यकताओं को पूरा करने में विफल रहते हैं, उत्पादन को समाप्त कर देगा।
जीएमपी प्रमाणन की मुख्य सामग्री दवा उत्पादन का गुणवत्ता प्रबंधन नियंत्रण है। इसकी सामग्री को दो भागों में संक्षेपित किया जा सकता है: सॉफ्टवेयर प्रबंधन और हार्डवेयर सुविधाएं। क्लीन रूम बिल्डिंग हार्डवेयर सुविधाओं में प्रमुख निवेश घटकों में से एक है। क्लीन रूम बिल्डिंग के पूरा होने के बाद, चाहे वह डिजाइन उद्देश्यों को प्राप्त कर सके और जीएमपी आवश्यकताओं को पूरा कर सके, अंततः परीक्षण के माध्यम से पुष्टि की जानी चाहिए।
क्लीन रूम के निरीक्षण के दौरान, उनमें से कुछ स्वच्छता निरीक्षण में विफल रहे, कुछ कारखाने के लिए स्थानीय थे, और कुछ पूरी परियोजना थीं। यदि निरीक्षण योग्य नहीं है, हालांकि दोनों पक्षों ने सुधार, डिबगिंग, सफाई आदि के माध्यम से आवश्यकताओं को प्राप्त किया है, तो यह अक्सर बहुत अधिक जनशक्ति और भौतिक संसाधनों को बर्बाद करता है, निर्माण अवधि में देरी करता है, और जीएमपी प्रमाणीकरण की प्रक्रिया में देरी करता है। परीक्षण से पहले कुछ कारणों और दोषों से बचा जा सकता है। हमारे वास्तविक काम में, हमने पाया है कि अयोग्य स्वच्छता और जीएमपी विफलता के मुख्य कारणों और सुधार उपायों में शामिल हैं:
1। अनुचित इंजीनियरिंग डिजाइन
यह घटना अपेक्षाकृत दुर्लभ है, मुख्य रूप से कम स्वच्छता आवश्यकताओं के साथ छोटे स्वच्छ कमरों के निर्माण में। क्लीन रूम इंजीनियरिंग में प्रतियोगिता अब अपेक्षाकृत उग्र है, और कुछ निर्माण इकाइयों ने परियोजना प्राप्त करने के लिए अपनी बोलियों में कम उद्धरण प्रदान किए हैं। निर्माण के बाद के चरण में, कुछ इकाइयों का उपयोग कोनों को काटने और उनके ज्ञान की कमी के कारण कम पावर एयर कंडीशनिंग और वेंटिलेशन कंप्रेसर इकाइयों का उपयोग करने के लिए किया गया था, जिसके परिणामस्वरूप बेमेल आपूर्ति शक्ति और स्वच्छ क्षेत्र होता है, जिसके परिणामस्वरूप अयोग्य सफाई होती है। एक और कारण यह है कि उपयोगकर्ता ने डिजाइन और निर्माण शुरू होने के बाद नई आवश्यकताओं और स्वच्छ क्षेत्र को जोड़ा है, जो मूल डिजाइन को आवश्यकताओं को पूरा करने में असमर्थ बना देगा। इस जन्मजात दोष में सुधार करना मुश्किल है और इसे इंजीनियरिंग डिजाइन चरण के दौरान बचा जाना चाहिए।
2। कम-अंत उत्पादों के साथ उच्च अंत उत्पादों की जगह
स्वच्छ कमरों में HEPA फ़िल्टर के आवेदन में, देश यह निर्धारित करता है कि 100000 या उससे अधिक के स्वच्छता स्तर के साथ वायु शोधन उपचार के लिए, प्राथमिक, मध्यम और HEPA फिल्टर के तीन-स्तरीय निस्पंदन का उपयोग किया जाना चाहिए। सत्यापन प्रक्रिया के दौरान, यह पाया गया कि एक बड़े स्वच्छ कमरे की परियोजना ने 10000 के स्वच्छता स्तर पर HEPA एयर फिल्टर को बदलने के लिए एक उप HEPA एयर फिल्टर का उपयोग किया, जिसके परिणामस्वरूप अयोग्य सफाई हुई। अंत में, जीएमपी प्रमाणन की आवश्यकताओं को पूरा करने के लिए उच्च दक्षता वाले फ़िल्टर को बदल दिया गया।
3। हवा की आपूर्ति वाहिनी या फ़िल्टर की खराब सील
यह घटना किसी न किसी निर्माण के कारण होती है, और स्वीकृति के दौरान, यह प्रतीत हो सकता है कि एक निश्चित कमरा या एक ही प्रणाली का हिस्सा योग्य नहीं है। सुधार विधि हवा की आपूर्ति वाहिनी के लिए रिसाव परीक्षण विधि का उपयोग करना है, और फ़िल्टर क्रॉस-सेक्शन, सीलिंग गोंद, और फ़िल्टर के स्थापना फ्रेम को स्कैन करने के लिए एक कण काउंटर का उपयोग करता है, रिसाव स्थान की पहचान करता है, और इसे सावधानी से सील करता है।
4। गरीब डिजाइन और वापसी हवा नलिकाओं या वायु vents का कमीशन
डिजाइन कारणों के संदर्भ में, कभी -कभी अंतरिक्ष सीमाओं के कारण, "टॉप सप्लाई साइड रिटर्न" या रिटर्न एयर वेंट की अपर्याप्त संख्या का उपयोग संभव नहीं है। डिजाइन कारणों को समाप्त करने के बाद, रिटर्न एयर वेंट्स का डिबगिंग भी एक महत्वपूर्ण निर्माण लिंक है। यदि डिबगिंग अच्छी नहीं है, तो रिटर्न एयर आउटलेट का प्रतिरोध बहुत अधिक है, और रिटर्न एयर वॉल्यूम सप्लाई एयर वॉल्यूम से कम है, यह अयोग्य स्वच्छता का कारण भी होगा। इसके अलावा, निर्माण के दौरान जमीन से वापसी एयर आउटलेट की ऊंचाई भी स्वच्छता को प्रभावित करती है।
5। परीक्षण के दौरान स्वच्छ कमरे प्रणाली के लिए अपर्याप्त आत्म शुद्धि समय
राष्ट्रीय मानक के अनुसार, शुद्धि एयर कंडीशनिंग प्रणाली सामान्य रूप से संचालित होने के 30 मिनट बाद परीक्षण प्रयास शुरू किया जाएगा। यदि चल रहे समय बहुत कम है, तो यह अयोग्य स्वच्छता का कारण भी बन सकता है। इस मामले में, यह एयर कंडीशनिंग शोधन प्रणाली के परिचालन समय को उचित रूप से बढ़ाने के लिए पर्याप्त है।
6। शुद्धि एयर कंडीशनिंग प्रणाली को अच्छी तरह से साफ नहीं किया गया था
निर्माण प्रक्रिया के दौरान, संपूर्ण शुद्धि एयर कंडीशनिंग प्रणाली, विशेष रूप से आपूर्ति और वापसी वायु नलिकाएं, एक बार में पूरी नहीं होती हैं, और निर्माण कर्मियों और निर्माण वातावरण वेंटिलेशन नलिकाओं और फिल्टर में प्रदूषण का कारण बन सकता है। यदि अच्छी तरह से साफ नहीं किया जाता है, तो यह सीधे परीक्षण के परिणामों को प्रभावित करेगा। सुधार का उपाय निर्माण करते समय साफ करना है, और पाइपलाइन की स्थापना के पिछले भाग के बाद पूरी तरह से साफ किया जाता है, पर्यावरणीय कारकों के कारण होने वाले प्रदूषण से बचने के लिए इसे सील करने के लिए प्लास्टिक फिल्म का उपयोग किया जा सकता है।
7। स्वच्छ कार्यशाला अच्छी तरह से साफ नहीं की
निस्संदेह, परीक्षण के आगे बढ़ने से पहले एक स्वच्छ कार्यशाला को अच्छी तरह से साफ किया जाना चाहिए। सफाई कर्मियों के मानव शरीर के कारण संदूषण को खत्म करने के लिए सफाई के लिए साफ काम के कपड़े पहनने के लिए अंतिम पोंछने वाले कर्मियों की आवश्यकता होती है। सफाई एजेंटों को नल का पानी, शुद्ध पानी, कार्बनिक सॉल्वैंट्स, तटस्थ डिटर्जेंट आदि हो सकते हैं। एंटी-स्टैटिक आवश्यकताओं वाले लोगों के लिए, एंटी-स्टैटिक लिक्विड में डूबा हुआ एक कपड़े के साथ अच्छी तरह से पोंछते हैं।
पोस्ट टाइम: जुलाई -26-2023